My RF1000 modifications (English)
Re: My RF1000 modifications (English)
Interesting design. I was always designing for two fans. Mainly because I was designing surround nozzle and I was already splitting airflow in half for that.
One thing I noticed is that axial fans loose a lot of power when you are using ducts and nozzles. The one I am using for part cooling is 45x45x10mm from old computer and the difference in airflow between blowing in free air and blowing through a nozzle is huge.
Consider radial fans. When I am going to make my next version, I will probably use those.
The thing I probably hate the most in this printer is that there is not enough space around hotend for any modifications.
One thing I noticed is that axial fans loose a lot of power when you are using ducts and nozzles. The one I am using for part cooling is 45x45x10mm from old computer and the difference in airflow between blowing in free air and blowing through a nozzle is huge.
Consider radial fans. When I am going to make my next version, I will probably use those.
The thing I probably hate the most in this printer is that there is not enough space around hotend for any modifications.
- rf1k_mjh11
- Developer
- Beiträge: 2107
- Registriert: Di 6. Jan 2015, 19:44
- Wohnort: Autriche
- Has thanked: 277 times
- Been thanked: 558 times
Re: My RF1000 modifications (English) - Hot End Design - Übergangszone
Promoz,
I agree with you on your interpretation of the basic design of the hot end. Here in the forum we called the zone between the hot and cold zone 'transition zone' (Übergangszone). But, although you may think that the ideal hot end would only contain a hot and a cold zone, the transition zone is currently an absolute requirement.
With the current design of a hot end, the feeding tube, in the hot end, needs to be larger than the filament, otherwise a lot of friction is created. Because the diameter of the tube is larger than the filament diameter, some means of sealing off the hot end chamber is required. Otherwise the molten plastic would flow upwards just as much as through the nozzle. This causes all kinds of problems, as some users here in the forum experienced, when they tried to use 1.75mm filament in a 3mm hot end.
An engineer could say there are other means of sealing the chamber, an O-ring, for example. This O-ring must deal with the following situation:
- fairly high temperatures (sorry - no natural rubber usable, also, probably no TPE material, either)
- fluctuating diameters of the filament (sorry - PTFE, Teflon is out, too, not enough flexibility)
That leaves us with high temperature silicone (with a really high friction value), and maybe some other exotic elastomers.
And even if we find a decent material for our O-ring, we're stuck with high wear, so we would have to change the O-ring regularly - not fun.
So, to make matters simple, the hot end design uses the filament itself, to seal off the hot from the cold zone. In the transition zone, the material softens, expands due to the forces, and seals off the feeder tube. There is no wear problem, because the 'seal' is constantly being replaced automatically. There is a slight problem with friction, which is why many hot end designs use Teflon in the area. The shorter the transition zone, the less friction you have, but a transition zone is needed, nevertheless.
A short transition zone can cause some problems with all-metal hot ends. If the required retract value pulls molten filament up into the cold zone, where it can instantly stick to the inside of the feeder tube, causing a terrible jam, which is very difficult to remove. (I have an all-metal hot end and I just experienced a jam like that due to my own fault.) I believe all-metall hot end manufacturers will begin using low-friction coating as a standard feature, soon, to eliminate this problem.
mjh11
I agree with you on your interpretation of the basic design of the hot end. Here in the forum we called the zone between the hot and cold zone 'transition zone' (Übergangszone). But, although you may think that the ideal hot end would only contain a hot and a cold zone, the transition zone is currently an absolute requirement.
With the current design of a hot end, the feeding tube, in the hot end, needs to be larger than the filament, otherwise a lot of friction is created. Because the diameter of the tube is larger than the filament diameter, some means of sealing off the hot end chamber is required. Otherwise the molten plastic would flow upwards just as much as through the nozzle. This causes all kinds of problems, as some users here in the forum experienced, when they tried to use 1.75mm filament in a 3mm hot end.
An engineer could say there are other means of sealing the chamber, an O-ring, for example. This O-ring must deal with the following situation:
- fairly high temperatures (sorry - no natural rubber usable, also, probably no TPE material, either)
- fluctuating diameters of the filament (sorry - PTFE, Teflon is out, too, not enough flexibility)
That leaves us with high temperature silicone (with a really high friction value), and maybe some other exotic elastomers.
And even if we find a decent material for our O-ring, we're stuck with high wear, so we would have to change the O-ring regularly - not fun.
So, to make matters simple, the hot end design uses the filament itself, to seal off the hot from the cold zone. In the transition zone, the material softens, expands due to the forces, and seals off the feeder tube. There is no wear problem, because the 'seal' is constantly being replaced automatically. There is a slight problem with friction, which is why many hot end designs use Teflon in the area. The shorter the transition zone, the less friction you have, but a transition zone is needed, nevertheless.
A short transition zone can cause some problems with all-metal hot ends. If the required retract value pulls molten filament up into the cold zone, where it can instantly stick to the inside of the feeder tube, causing a terrible jam, which is very difficult to remove. (I have an all-metal hot end and I just experienced a jam like that due to my own fault.) I believe all-metall hot end manufacturers will begin using low-friction coating as a standard feature, soon, to eliminate this problem.
mjh11
RF1000 (seit 2014) mit:
Pico Hot End (mit eigenem Bauteil- und Hot End Lüfter)
Ceran Bett
FW RF.01.47 (von Conrad, modif.)
Die Natur kontert immer sofort mit einem besseren Idioten.
Pico Hot End (mit eigenem Bauteil- und Hot End Lüfter)
Ceran Bett
FW RF.01.47 (von Conrad, modif.)
Die Natur kontert immer sofort mit einem besseren Idioten.
Re: My RF1000 modifications (English)
Thanks for the explanation. I didn't even think before about this seal to prevent the upward flow.
And while we are on topic on hotends, and If I understand correctly you are developer at Conrad:
I was looking at hotends of new RF100 and RF500. They are both different. RF100 one looks a lot like so called MK8 extruder that is usually sold in chinese printers, while RF500 one looks like a new design.
My question is : why didn't you go with E3D Lite6 hotend? I my opinion developing your own hotend and manufacturing it in relatively small series must be more expensive than buying 35€ hotend (even cheaper if you buy a lot of them)? What is wrong with existing hotends on the market that you can do better?
And while we are on topic on hotends, and If I understand correctly you are developer at Conrad:
I was looking at hotends of new RF100 and RF500. They are both different. RF100 one looks a lot like so called MK8 extruder that is usually sold in chinese printers, while RF500 one looks like a new design.
My question is : why didn't you go with E3D Lite6 hotend? I my opinion developing your own hotend and manufacturing it in relatively small series must be more expensive than buying 35€ hotend (even cheaper if you buy a lot of them)? What is wrong with existing hotends on the market that you can do better?
- rf1k_mjh11
- Developer
- Beiträge: 2107
- Registriert: Di 6. Jan 2015, 19:44
- Wohnort: Autriche
- Has thanked: 277 times
- Been thanked: 558 times
Re: My RF1000 modifications (English)
Primoz,
I am honored that you think I am a developer at Conrad, but that is not true. "Developer" is just a category I was put in by the forum because of my many posts
. I bought my first 3D printer in 2011, a Mendel. It still sits on my desk but doesn't get a lot of exercise.
Two forum members who do work at Conrad are RF1000, who knows a lot about the firmware (he may be the developer of it?), and Marcometaner, who is more of a hardware guy.
Maybe they can help you with your questions - no guarantees, though.
Some of my thoughts, however:
mjh11
I am honored that you think I am a developer at Conrad, but that is not true. "Developer" is just a category I was put in by the forum because of my many posts


Two forum members who do work at Conrad are RF1000, who knows a lot about the firmware (he may be the developer of it?), and Marcometaner, who is more of a hardware guy.
Maybe they can help you with your questions - no guarantees, though.
Some of my thoughts, however:
We could ask the very same question to Mercedes, VW, BMW, Hyundai, Fiat, Ford, Toyota ....., regarding the development of an engine. There are already so many good engines out there. Why spend millions and years developing a new engine, when there already are so many existing (good) designs to choose from?Primoz hat geschrieben:What is wrong with existing hotends on the market that you can do better?
mjh11
RF1000 (seit 2014) mit:
Pico Hot End (mit eigenem Bauteil- und Hot End Lüfter)
Ceran Bett
FW RF.01.47 (von Conrad, modif.)
Die Natur kontert immer sofort mit einem besseren Idioten.
Pico Hot End (mit eigenem Bauteil- und Hot End Lüfter)
Ceran Bett
FW RF.01.47 (von Conrad, modif.)
Die Natur kontert immer sofort mit einem besseren Idioten.
Re: My RF1000 modifications (English)
I wasn't sure if you are a developer or it is just a category. (The rest of us only have stars and you have a banner).
I don't think it is fair to compare Conrad with cars manufacturers. Firstly cars manufactures have a 100 years of heritage, mixed with national pride and all that social-economics stuff. Secondly they sell enough cars to cover their costs and thirdly there is no "universal" engine that could fit in a car with just a different bracket (you have to consider transmission, cooling, ...). I don't know how much printers they sell or plan to sell, but compared to ultimaker, makerbot or Prusa, I think they are more boutique manufacturers (if we have to compare it with cars, let say Caterham, Lotus and even Pagani didn't make their own engines at the beginning. And with RF500 they are entering in middle-lower range, so they are more like Dacia).
And in engineering school we were taught to buy as many as possible of pre-made parts as they are cheaper (if they are made in high volumes) and focus your time and money on other stuff.
I am assuming that the new hotend on RF500 is costing them more then Lite6 (I think they could get it for less than 20€/piece without tax). Of course if it is cheaper then this is a good reason. But considering they sell V2 for 85€, I doubt that.
And during a development you are supposed to test things that are already on the market, so I am assuming they tested Lite6, to which I am also interested to know if anything is wrong with it.
Not to get too much off topic, here are some pictures of my previous attempts of cooling the cold end and surround nozzle.
This was the first one. First the white part was made for cooling cold end. I used it for a while with stock part cooling fan. Then I also made surround nozzle.


Second version:


Third version: Here a bottom part with surround nozzle is missing. It was supposed to be changeable surround nozzle, so I could find the best geometry. Those were made from PLA which worked fine when printing PLA, But then I tried to print ABS and a heat from the bed warped it. At that point I made aluminium sheet one that is currently in use.
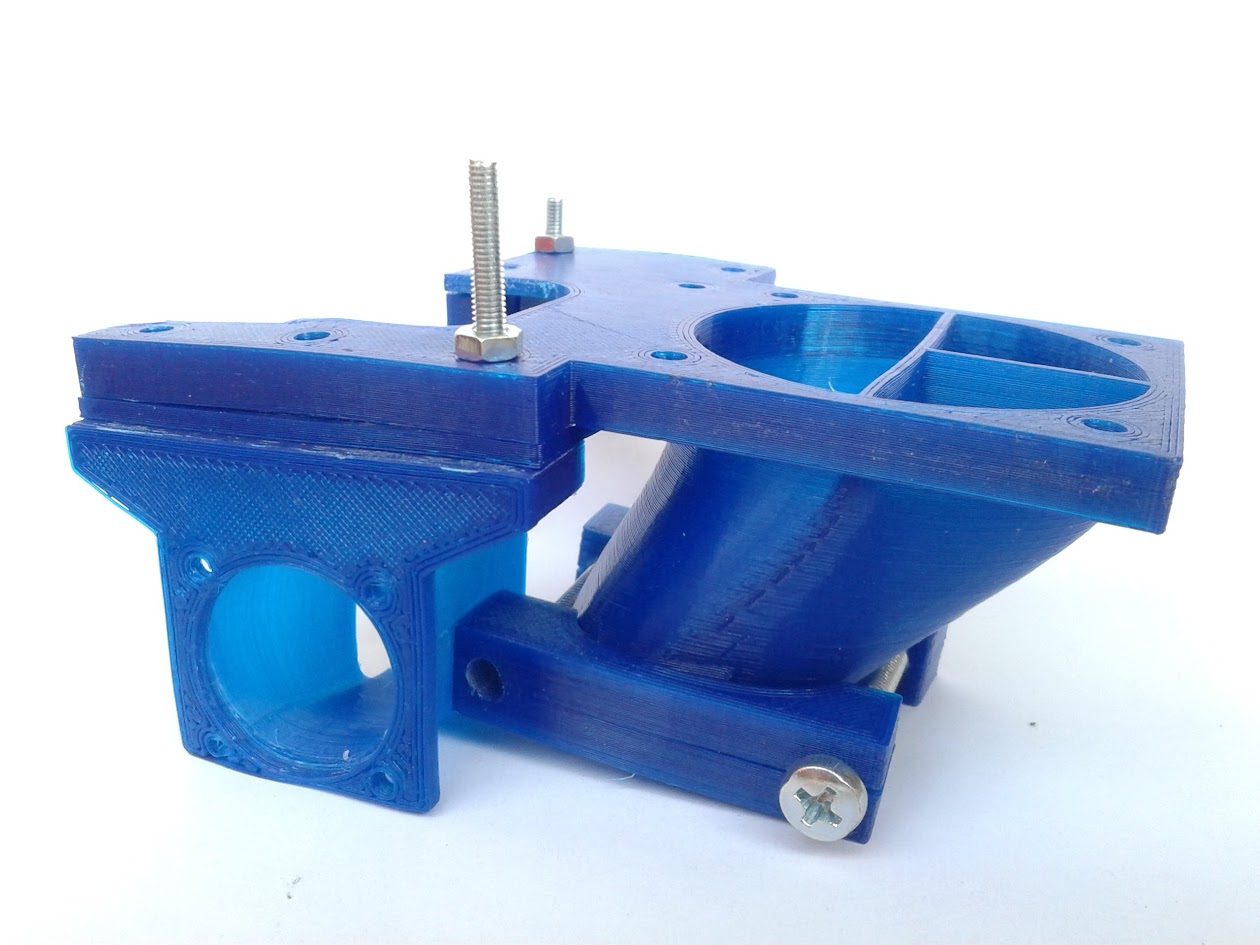

I don't think it is fair to compare Conrad with cars manufacturers. Firstly cars manufactures have a 100 years of heritage, mixed with national pride and all that social-economics stuff. Secondly they sell enough cars to cover their costs and thirdly there is no "universal" engine that could fit in a car with just a different bracket (you have to consider transmission, cooling, ...). I don't know how much printers they sell or plan to sell, but compared to ultimaker, makerbot or Prusa, I think they are more boutique manufacturers (if we have to compare it with cars, let say Caterham, Lotus and even Pagani didn't make their own engines at the beginning. And with RF500 they are entering in middle-lower range, so they are more like Dacia).
And in engineering school we were taught to buy as many as possible of pre-made parts as they are cheaper (if they are made in high volumes) and focus your time and money on other stuff.
I am assuming that the new hotend on RF500 is costing them more then Lite6 (I think they could get it for less than 20€/piece without tax). Of course if it is cheaper then this is a good reason. But considering they sell V2 for 85€, I doubt that.
And during a development you are supposed to test things that are already on the market, so I am assuming they tested Lite6, to which I am also interested to know if anything is wrong with it.
Not to get too much off topic, here are some pictures of my previous attempts of cooling the cold end and surround nozzle.
This was the first one. First the white part was made for cooling cold end. I used it for a while with stock part cooling fan. Then I also made surround nozzle.
Second version:
Third version: Here a bottom part with surround nozzle is missing. It was supposed to be changeable surround nozzle, so I could find the best geometry. Those were made from PLA which worked fine when printing PLA, But then I tried to print ABS and a heat from the bed warped it. At that point I made aluminium sheet one that is currently in use.
-
- Profi 3D-Drucker
- Beiträge: 465
- Registriert: So 7. Feb 2016, 11:04
- Wohnort: Rinteln
- Has thanked: 16 times
- Been thanked: 238 times
Re: My RF1000 modifications (English)
Hi,
I dont think so sophisticated. I just look at what happens and try to explain it for myself. And I noticed that the filament gets mold after some time of printing. So it often happened, that the first part of a print was fine and then air printing started when printing ABS. Increasing pressure make it a bit better, but i am shure, that this overstresses the stepper by the long run. So i think it is really important to cool the upper extruder part including the gear. So i made this quite simple design. I cant say yet if it finally solves some of the problems, but i think it should. Thats how it looks like:
All seems to work (hbs is running atm). I will do first test prints tomorrow.
PeterKa
PS: Of course the stl files are public for free.
I dont think so sophisticated. I just look at what happens and try to explain it for myself. And I noticed that the filament gets mold after some time of printing. So it often happened, that the first part of a print was fine and then air printing started when printing ABS. Increasing pressure make it a bit better, but i am shure, that this overstresses the stepper by the long run. So i think it is really important to cool the upper extruder part including the gear. So i made this quite simple design. I cant say yet if it finally solves some of the problems, but i think it should. Thats how it looks like:
All seems to work (hbs is running atm). I will do first test prints tomorrow.
PeterKa
PS: Of course the stl files are public for free.
Du hast keine ausreichende Berechtigung, um die Dateianhänge dieses Beitrags anzusehen.
-
- Profi 3D-Drucker
- Beiträge: 415
- Registriert: Sa 18. Okt 2014, 22:20
- Has thanked: 84 times
- Been thanked: 69 times
Re: My RF1000 modifications (English)
I have switched to the e3d full metal hotend (1) since a while and had not that much problems. Then i convered to the e3d titan extruder for printing flexible tpe material and ran into similar issues. So i installed a switchable (4) fan (3 )for the drive gear and filament supply and it works. I think it would also be a very good thing to cool the extruder motor itself, maybe by watercooling or something cause it generates a lot if heat..
And it still fits when housing is closed for printing abs. The fan 3 can be turned off then.
And it still fits when housing is closed for printing abs. The fan 3 can be turned off then.
Du hast keine ausreichende Berechtigung, um die Dateianhänge dieses Beitrags anzusehen.
E3DV6+Titan Total Conversion
Aluheizbett + MTPlus + zweite Y-Schiene mit Wagen
Z-Kette
X-kette
Platinenlüfter
X19 Schaltung LED
pi-Octopi+ Cam
Ritzel-Kühler
Firmware Mod 1.45.00
Aluheizbett + MTPlus + zweite Y-Schiene mit Wagen
Z-Kette
X-kette
Platinenlüfter
X19 Schaltung LED
pi-Octopi+ Cam
Ritzel-Kühler
Firmware Mod 1.45.00
Re: My RF1000 modifications (English)
I also had a hot extruder stepper motor (and also y and x motor). I mounted a fan on extruder motor (you can see it on pictures on previous page), but because it is 12V fan and is running from the same 7,5V power supply as my cold end fan, it barely spins and it doesn't blow much. After that I lowered stepper current for all motors in firmware and that seems to help. After that I didn't pay much attention to that, as I didn't have problems anymore. Today I touched a motor after I read your posts and It was hot, but not too hot to touch. I was printing ABS for couple of months now, but before that I was printing PLA, but it got me thinking that, If it was that hot, how didn't it make problems then?
Now I think that the heat from the bed might be a part of the problem. With PLA 55°C and with ABS 95°C. The whole plate is aluminium and is a good heat conductor so the heat quickly spreads to rail, carriage and then also extruder motor. Of course extruder motor then adds its own heat.
If this would be true, then it would also be a difference in temperature of extruder when printing high part with small footprint vs. low part with big footprint.
Now this is just something that came to my mind and would have to be tested.
@PeterKa
Is that PEI sheet on your bed? Where did you buy it?
@Wessix
I am surprised you manage to fit that fan there (number 2)? Is your x axis now smaller or can you still print to the edge of the bed?
Now I think that the heat from the bed might be a part of the problem. With PLA 55°C and with ABS 95°C. The whole plate is aluminium and is a good heat conductor so the heat quickly spreads to rail, carriage and then also extruder motor. Of course extruder motor then adds its own heat.
If this would be true, then it would also be a difference in temperature of extruder when printing high part with small footprint vs. low part with big footprint.
Now this is just something that came to my mind and would have to be tested.
@PeterKa
Is that PEI sheet on your bed? Where did you buy it?
@Wessix
I am surprised you manage to fit that fan there (number 2)? Is your x axis now smaller or can you still print to the edge of the bed?
-
- Profi 3D-Drucker
- Beiträge: 465
- Registriert: So 7. Feb 2016, 11:04
- Wohnort: Rinteln
- Has thanked: 16 times
- Been thanked: 238 times
Re: My RF1000 modifications (English)
Hi, I dont know what PEI means. The sheet is from hardpaper manufactured by 3M. In Germany it is sold for huge prizes by Filaprint. I buy it from amazone where 5 sheets 12''x12'' are sold for 16€. Just google "3M 486MP". Its very handy and really solves most warping issues. Bed temperature must be below 120 degrees but thats enough for abs. With this sheet i dont need to use stick or ABS juice.
PeterKa
PeterKa
- Nibbels
- Developer
- Beiträge: 2264
- Registriert: Mi 17. Aug 2016, 17:01
- Has thanked: 831 times
- Been thanked: 599 times
Re: My RF1000 modifications (English)
I checked this and found 3M 468 MP @16€ only. Even within the following datrasheet, there is no 486. Therefore I suspect a numbertwist at this point.PeterKa hat geschrieben:"3M 486MP"
https://multimedia.3m.com/mws/media/104 ... -200mp.pdf
And there is something called PEI:
https://www.amazon.com/Polyetherimide-N ... ZED92W172D
Greetings
RF2000
Firmware Mod 1.45.00.Mod - geht SD wieder 100%?
Bitte 1.42.17 bis 1.42.21 meiden!
SD-Druck mit der Community-FW <= 1.43.99 aktuell meiden.
Firmware Mod 1.45.00.Mod - geht SD wieder 100%?
Bitte 1.42.17 bis 1.42.21 meiden!
SD-Druck mit der Community-FW <= 1.43.99 aktuell meiden.